Incremental Flow Testing
It is therefore highly desirable to measure the flow coming not only from an entire borehole but from each section of a borehole. The process shown in Figure 1 can be used to determine the flow at various locations along shorter holes. Here, a single seal (packer) is pushed to the back of the hole and then inflated, before the flow is measured. The packer is then deflated and moved out by say a test rod length, before being re-inflated and the flow measured again. The flow per unit length is therefore the difference between measurements, or the slope of the flow versus distance curve. This process may be repeated over the length of the hole to get a complete flow profile.
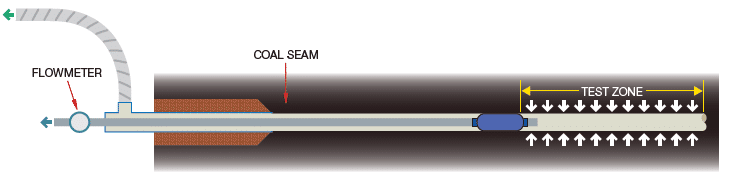
In longer holes, this approach cannot be used because the change in flow between measurements is small compared to total flow. The system shown in Figure 2 is therefore used. In this system, straddle packers (two seals with a test zone between them) are inflated to isolate a section of hole and measure its flow. The flow from inner zone of the hole is bypassed past the straddle packer system.
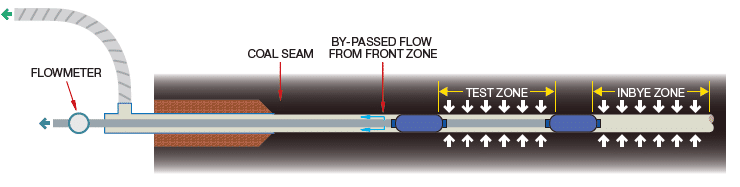
Determining Permeability
The quickest experimental method to determine the permeability of gassy coal seams is to use the system shown in Figure 3.
Here a hole is drilled and a single packer is inserted beyond the crushed zone near the underground roadway to seal the hole. All the flow comes down the test tubing, which is connected to the packer. The flow of water and gas is measured over a period and then the valve on the tubing is closed and the pressure build-up is monitored. It is usual to repeat this for a second flow and build up period. The test technique can be conducted in holes of several orientations so as to determine the directional characteristics of permeability. The exact nature of the permeability must be determined by history matching and using a simulator, because of the complex behaviour of coal seams.
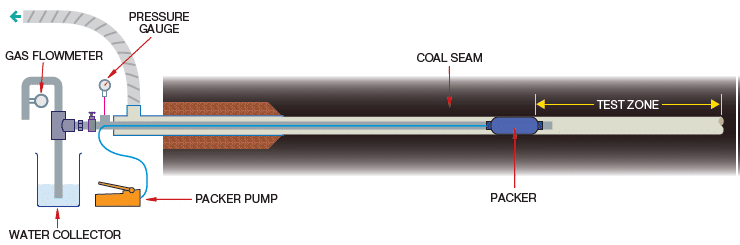
Where only a single fluid is being produced, the testing procedure becomes easier as gas and water separation is not required.
For longer holes, it is not practical to manually push a packer up the hole, thus a system to operate with the drill string is required. A setup such as that shown in Figure 4 is required.

Much as with testing from holes drilled from surface to a reservoir it is, in cases, desirable to be able to monitor the changing pressures from underground. Sigra can do this through the installation of pressure sensors from underground. An example of a layout used for this is shown in Figure 5. Here the outer bore holes act as cut offs for lateral flow while the two central holes act as part of a drainage pattern monitored by a central hole with cemented in pressure sensors.
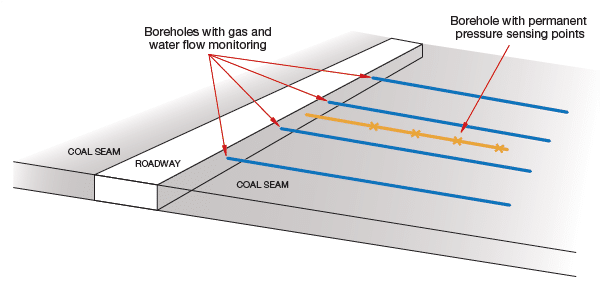